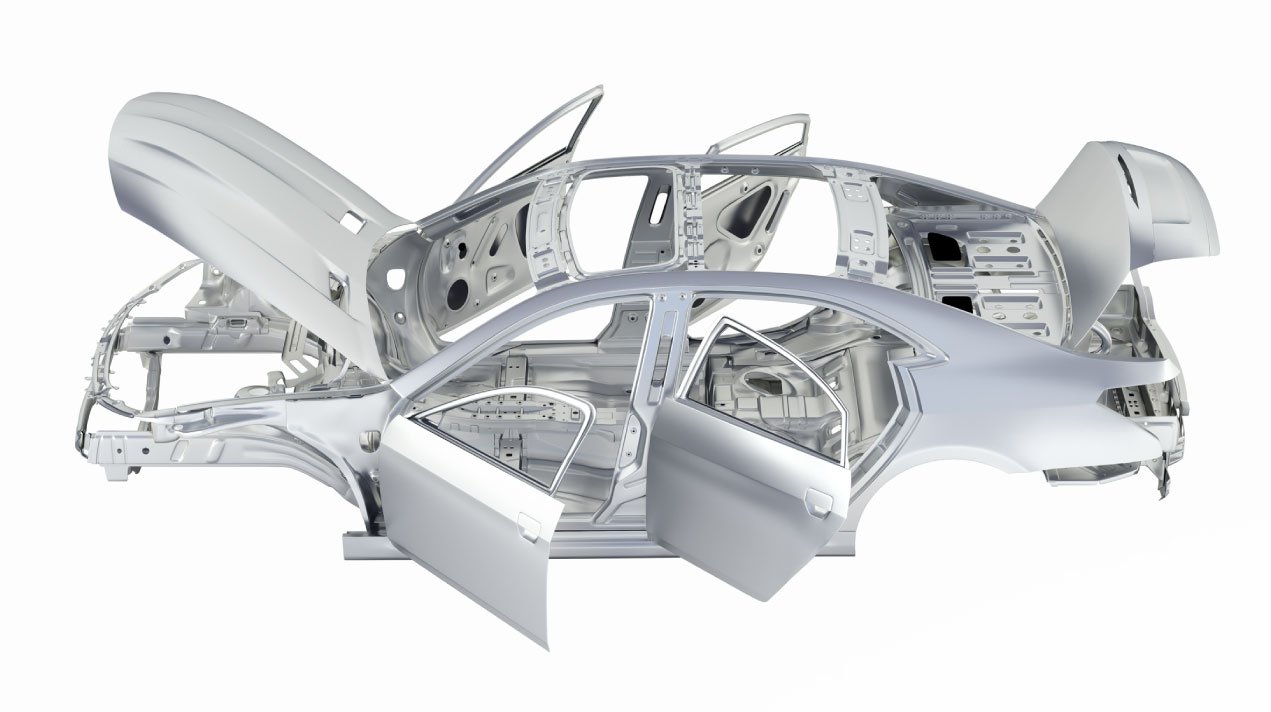
R&D Project Spotlight: Vehicle Design for High-Value Recycling of Aluminum
The embodied energy of vehicles is increasing as energy‐intensive materials such as aluminum auto body sheet (ABS) are used to deliver improved performance. Unfortunately, the current system cannot effectively recycle automotive aluminum at end-of life (EOL) because the shredded aluminum is frequently contaminated with steel rivets, steel alloys, and copper wiring. As a result, 90% of auto shred aluminum is exported and downcycled.
In addition, the shift to electric vehicles (EVs) will increase the demand for high‐quality aluminum ABS and advanced high strength steels (AHSS) for light weighting, double the amount of copper wire (thereby increasing end-of-life contamination), and potentially reduce demand for vehicle castings that could utilize the lower quality scrap.
To address these end-of-life issues upfront, the R&D project team is developing a new design for recycling tool that considers how vehicle design, recycling system infrastructure, and sheet manufacturing process decisions impact factors such as EOL recycled content, closed and open‐loop recycling rates, greenhouse gas (GHG) emissions, and primary feedstock consumption and energy demand under different scenarios from 2020‐2050 (e.g. rapid deployment of EVs).
The tool will be integrated into the Argonne National Laboratory (ANL) GREET model, which is already widely used by the car industry to quantify environmental impacts. Once developed and implemented, this tool has the potential to reduce the consumption of primary steel and aluminum by 2.35 million metric tons (MMT) and 0.19 MMT, respectively.
Project Lead:
University of Michigan
Project Participants:
Ford, Novelis, Argonne National Laboratory, The Aluminum Association, ISRI, Light Metal Consultants